Solutions
Solutions
Case04
Minimizing Warpage
The Many Causes of Warpage
In today’s manufacturing industry, high demand for precise parts often equates to tolerances of less than 0.01mm.
Such small tolerance is a concern when hardening parts because of unavoidable warpage.
Major causes of warpage are:
・release of residual stress
・change of structural composition
Parts undergo various processes before hardening.
The raw material undergoes stretching, forging, tapping, molding and cutting, all which create stress.
This stress, pulling and pushing on the part from the inside, is released when heated, causing warpage.
Fig.1 Stress Concentration
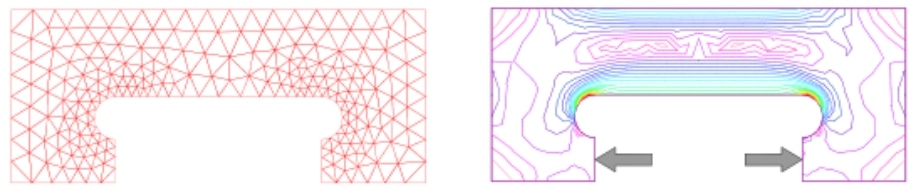
Hardening also alters the structural composition of the part.
When steel is heated above 911℃, the nuclear structure changes from body-centered cubic (BCC) to face-centered cubic (FCC).
This affects the amount of space taken up by and distance between atoms, causing the steel to expand and deform in unpredictable ways.
※ Amount of expansion depends on carbon content.
Adding a grinding margin to achieve desired dimensions is an extra process and is difficult for knurling and angled surfaces.
Altering the part dimensions before hardening to account for warpage is also difficult to reproduce constantly.
Straightening with too much force can cause cracking and reduce the part’s hardness.
At Fuji Denshi, we have developed original IH technology that solves these problems and minimizes warpage for various parts.
For customers using atmosphere processing, we highly recommend switching to our IH hardening.
Fig.2 BCC, FCC Structure
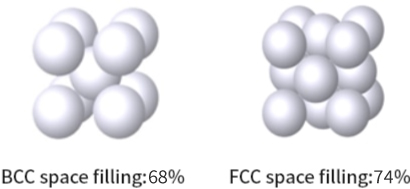
▲